Was sind MEMS (mikro-elektromechanische Systeme)?
MEMS, oder mikro-elektromechanische Systeme, repräsentieren eine bahnbrechende Technologie an der Schnittstelle zwischen Mechanik und Elektronik. Diese Miniaturmaschinen integrieren sowohl mechanische als auch elektronische Komponenten auf mikroskopischer Ebene. Die Dimensionen eines MEMS können von einigen Millimetern bis zu unter einem Mikrometer reichen – deutlich kleiner als die Breite eines menschlichen Haares (ca. 70 μm). Diese bemerkenswerte Miniaturisierung ermöglicht die Integration komplexer Funktionalitäten auf kleinsten Raum.
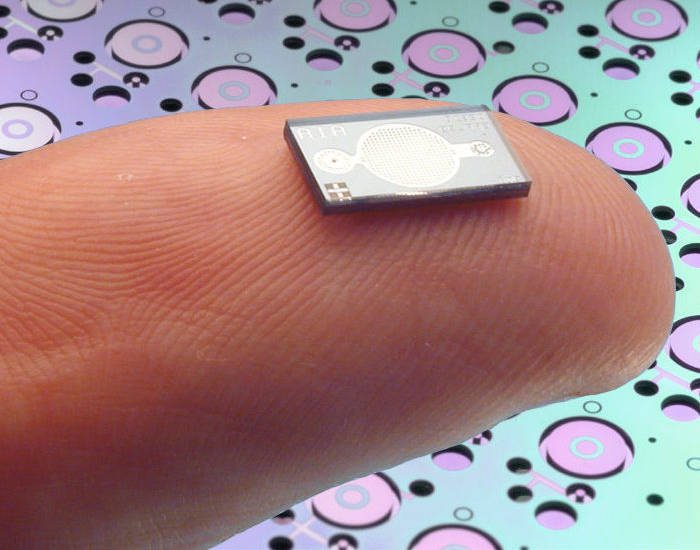
Der Begriff MEMS bezieht sich sowohl auf die Kategorie dieser mikromechanischen Geräte als auch auf die spezifischen Herstellungsverfahren. Interessanterweise müssen MEMS nicht zwingend bewegliche Teile enthalten, um als solche klassifiziert zu werden. Entscheidend ist vielmehr die Miniaturisierung von strukturellen Elementen wie Federn, Kanälen, Hohlräumen, Löchern oder Membranen, die auch in konventionellen Maschinen Verwendung finden. Da viele MEMS-Geräte mechanische Signale in elektrische oder optische Signale umwandeln, werden sie häufig auch als Wandler bezeichnet.
Die Terminologie variiert regional: In Japan sind diese Technologien eher als „Mikromaschinen“ bekannt, während in Europa der Begriff „Mikrosystemtechnik“ (MST) gebräuchlicher ist.
Aufbau und Struktur von MEMS
Die Architektur eines MEMS-Geräts umfasst typischerweise mehrere Schlüsselkomponenten:
- Mikrosensoren: Diese erfassen physikalische Daten aus der Umgebung
- Mikroprozessoren: Verarbeiten die gesammelten Daten
- Mikroaktuatoren: Wandeln Energie in mechanische Bewegung um
- Datenverarbeitungseinheiten: Führen Berechnungen und logische Operationen durch
- Schnittstellen: Ermöglichen die Interaktion mit externen Systemen
Im Gegensatz zu herkömmlichen mechatronischen Systemen werden MEMS überwiegend mit den gleichen Massenfertigungstechniken produziert, die auch bei der Herstellung integrierter Schaltkreise (ICs) zum Einsatz kommen. Dies stellt einen signifikanten Kostenvorteil dar. Viele kommerzielle MEMS-Produkte werden direkt mit ICs integriert und gemeinsam verpackt. Diese Integrationsmöglichkeit von Sensoren und Aktuatoren auf demselben Substrat ist ein besonderer Vorteil der MEMS-Fertigung.
Komponentenklasse | Typische Größenordnung | Funktionsbeschreibung | Beispielanwendungen |
---|---|---|---|
Mikrosensoren | 1-100 μm | Umwandlung physikalischer Phänomene in elektrische Signale | Beschleunigungssensoren, Drucksensoren |
Mikroaktuatoren | 10-500 μm | Umwandlung von Energie in mechanische Bewegung | Mikropumpen, Mikroventile |
Mikrostrukturelemente | 0,5-50 μm | Passive mechanische Funktionen | Mikrokanäle, Membranen |
Mikroelektronik | 0,01-10 μm | Signalverarbeitung und Steuerung | Integrierte Schaltkreise, ASICs |
Herstellungsprozesse
Die Fertigung von MEMS basiert auf einer Kombination spezialisierter Prozesse, die aus der Halbleiterfertigung abgeleitet wurden. Diese umfassen:
- Photolithographie: Präzises Übertragen von Mustern auf Siliziumsubstrat
- Ätzen: Selektives Entfernen von Material zur Erzeugung dreidimensionaler Strukturen
- Nassätzen: Einsatz chemischer Lösungen (Ätzrate: 1-10 μm/min)
- Trockenätzen: Verwendung reaktiver Gase (Ätzrate: 0,1-5 μm/min)
- Abscheidung: Aufbringen dünner Schichten diverser Materialien
- Chemische Gasphasenabscheidung (CVD): Schichtdicken von 0,01-10 μm
- Physikalische Gasphasenabscheidung (PVD): Schichtdicken von 0,01-5 μm
- Waferbonden: Verbinden mehrerer Substrate zu komplexen 3D-Strukturen
- Oberflächenmikromechanik: Erzeugung beweglicher Strukturen durch selektives Entfernen von Opferschichten
- Volumenmikromechanik: Strukturierung des gesamten Substratvolumens
Die industrielle Fertigung nutzt 150-300 mm Siliziumwafer mit Strukturgenauigkeiten im Submikrometerbereich und erlaubt die parallele Produktion tausender identischer Geräte pro Wafer.
Trotz niedriger Stückkosten stellt die Verpackung von MEMS eine technische Herausforderung dar. Die Geräte müssen so verpackt werden, dass die elektrischen oder optischen Schaltkreise vor Umwelteinflüssen wie Luft und Feuchtigkeit geschützt sind, während bestimmte Komponenten dennoch mit der Umgebung interagieren und mechanische Bewegungen ausführen können.
Anwendungsgebiete und Beispiele
Die Vielseitigkeit von MEMS zeigt sich in ihrer breiten Anwendungspalette. Ein alltägliches Beispiel ist das System-on-Chip (SoC), das die automatische Bildschirmausrichtung in Smartphones steuert. Mit der kontinuierlichen Miniaturisierung, Reduzierung des Energieverbrauchs und sinkenden Fertigungskosten wird erwartet, dass MEMS eine Schlüsselrolle im Internet der Dinge (IoT) und in der Hausautomatisierung spielen werden.
Automobilindustrie
In modernen Fahrzeugen sind mindestens 50 MEMS-Geräte verbaut, die essentielle Bestandteile verschiedener Sicherheitssysteme bilden:
- Airbag-Steuerungen: Beschleunigungssensoren mit Messbereich von ±50g und Reaktionszeiten <10 ms
- Elektronische Stabilitätskontrolle (ESC): Gyroskope mit Messraten von 100-1000°/s
- Reifendruckkontrollsysteme (TPMS): Drucksensoren mit Messbereich von 0-600 kPa und Genauigkeit von ±10 kPa
Konsumelektronik
- Mikrospiegel-Arrays: Ermöglichen hochauflösende Projektionssysteme mit über 2 Millionen einzeln steuerbarer Spiegel
- Smartphone-Sensoren: Beschleunigungsmesser, Gyroskope, Magnetometer, Barometer mit Messauflösungen im Bereich von 0,1-0,01% des Messbereichs
- Mikrofone: MEMS-Mikrofone mit Frequenzbereich von 20 Hz – 20 kHz und Signal-Rausch-Verhältnis >65 dB
Medizintechnik
Ein bemerkenswertes Beispiel im medizinischen Bereich ist die von Debiotech und STMicroelectronics entwickelte tragbare Einweg-Insulinpumpe zur Diabetesbehandlung. Der Chip besteht aus drei miteinander verbundenen Schichten:
- Einer Silizium-auf-Isolator-Platte (SOI) mit mikrobearbeiteten Pumpenstrukturen
- Zwei Silizium-Deckplatten mit präzisen Durchgangslöchern
Ein piezoelektrischer Aktor auf dem Chip bewegt eine Membran in oszillierender Bewegung, um die Flüssigkeit in der Pumpkammer zu komprimieren und zu dekomprimieren. Diese Pumpe kann Insulindosen mit einer Präzision von ±5% im Dosierungsbereich von 0,1-10 IU/h abgeben.
Weitere medizinische Anwendungen umfassen:
- Einweg-Drucksensoren: Für die Blutdrucküberwachung mit Messbereichen von 0-300 mmHg
- Lab-on-a-Chip-Systeme: Miniaturisierte Analysegeräte mit Probenvolumina im Nanoliter-Bereich
- Implantierbare Sensoren: Zur kontinuierlichen Überwachung von Vitalparametern mit Lebensdauern >5 Jahre
Industrielle Anwendungen
- Sensorgesteuerte HLK-Systeme: Für Gebäudemanagementsysteme mit Energieeinsparungen von 15-30%
- Intelligenter Staub: Zur Erkennung von Umweltveränderungen in Reinräumen mit Partikeldetektion <0,1 μm
- Mikrodüsen: Zur präzisen Steuerung des Tintenflusses in Tintenstrahldruckern mit Tropfenvolumina von 1-30 pl
- Optische Schaltgeräte: Mit Schaltzeiten <1 ms und Dämpfungen <0,5 dB
Anwendungsbereich | Typische Leistungsparameter | Marktvolumen 2023 (Mrd. USD) | Prognostizierte jährliche Wachstumsrate |
---|---|---|---|
Automobilindustrie | Betriebstemperatur: -40 bis +125°C | 4,7 | 8,5% |
Konsumelektronik | Leistungsaufnahme: 10-100 μW | 6,3 | 12,2% |
Medizintechnik | Sterilisierbarkeit: >100 Zyklen | 2,8 | 15,7% |
Industrielle Anwendungen | MTBF: >50.000 Stunden | 5,1 | 9,3% |
Historische Entwicklung
Die konzeptionelle Idee zur Entwicklung von MEMS entstand in den 1980er Jahren, jedoch waren die technologischen Voraussetzungen für Design und Herstellung erst in den 1990er Jahren ausreichend verfügbar. Zu den ersten kommerziell erfolgreichen MEMS-Anwendungen zählten Airbag-Steuerungen und Tintenstrahldruckköpfe. Ende der 1990er Jahre folgten Projektoren mit Mikrospiegeln, die MEMS-Technologie nutzten.
Eine signifikante Rolle in der Frühphase der MEMS-Entwicklung spielte die Defense Advanced Research Projects Agency (DARPA) über ihr Research and Development Electronics Technology Office, das substanzielle finanzielle Unterstützung für Grundlagenforschung bereitstellte.
Meilensteine in der MEMS-Entwicklung:
- 1967: Erstes Silizium-Drucksensorelement (Honeywell)
- 1979: Erstes mikromechanisches Inkjet-Druckkopfelement (HP)
- 1982: Erste oberflächenmikromechanische Strukturen (Berkeley)
- 1991: Kommerzialisierung von MEMS-Beschleunigungssensoren für Airbags
- 1996: Einführung des Digital Micromirror Device (DMD) für Projektoren (Texas Instruments)
- 2001: Marktdurchbruch von MEMS-Gyroskopen für Fahrstabilitätssysteme
- 2007: Massenproduktion von MEMS für Smartphones beginnt
- 2015: Integration von MEMS in Wearables und IoT-Geräte
- 2020: Erste vollintegrierte MEMS mit KI-Funktionalität auf einem Chip
Im Laufe der Zeit wurden Mikrosensoren für eine Vielzahl von Sensortypen entwickelt, darunter Sensoren für Temperatur (Messbereich: -55 bis +150°C, Auflösung: 0,01°C), Druck (Messbereich: 0-10 MPa, Auflösung: 100 Pa), Magnetfelder (Messbereich: ±8 mT, Auflösung: 0,1 μT) und Strahlung. In vielen Fällen erwiesen sich Sensoren auf MEMS-Basis als deutlich leistungsfähiger im Vergleich zu ihren makroskopischen Gegenstücken.
MEMS vs. NEMS – Der Schritt zum Nanometer-Bereich
Während MEMS für mikro-elektromechanische Systeme steht, repräsentieren NEMS (nano-elektromechanische Systeme) eine weitere Miniaturisierungsstufe. NEMS werden in der Nanotechnologie eingesetzt, die Materie auf atomarer oder molekularer Ebene manipulieren kann. Bei einem Top-down-Ansatz in der Nanotechnologie kommen Fertigungstechniken zum Einsatz, die denen der MEMS-Technologie ähneln.
Obwohl MEMS und NEMS gelegentlich als separate Technologiefelder betrachtet werden, sind sie in Wirklichkeit eng miteinander verknüpft und voneinander abhängig. MEMS-Technologien bilden häufig die Grundlage für die Entwicklung von NEMS-Anwendungen. Ein anschauliches Beispiel ist das Rastertunnelmikroskop (STM), das einzelne Atome detektieren kann und selbst ein MEMS-Gerät darstellt.
Vergleichende technische Spezifikationen:
- MEMS:
- Strukturgrößen: 1-100 μm
- Typische Materialien: Silizium, Polysilizium, Siliziumdioxid, Metalle
- Fertigungsverfahren: Standardprozesse der Halbleiterindustrie
- Energieverbrauch: 10 μW – 10 mW
- Ansprechzeit: 1 μs – 1 ms
- NEMS:
- Strukturgrößen: 1-100 nm
- Typische Materialien: Kohlenstoffnanoröhren, Graphen, Quantenpunktstrukturen
- Fertigungsverfahren: Spezielle Nanolithographie, Selbstorganisation
- Energieverbrauch: 1 nW – 1 μW
- Ansprechzeit: 1 ns – 1 μs
Zukunftsperspektiven und Herausforderungen
Die MEMS-Technologie steht an der Schwelle zu neuen Anwendungsgebieten, die durch fortschreitende Miniaturisierung, erhöhte Funktionsdichte und verbesserte Energieeffizienz ermöglicht werden. Aktuelle Forschungsansätze konzentrieren sich auf:
- Integration mit Künstlicher Intelligenz: Entwicklung intelligenter Sensornetzwerke mit On-Chip-Datenverarbeitung
- Biomedizinische Implantate: Mikrosysteme zur gezielten Wirkstoffabgabe mit Dosiergenauigkeiten im Nanoliter-Bereich
- Energieautarke MEMS: Integrierte Energy-Harvesting-Funktionen mit Leistungsdichten >100 μW/cm²
- Quantensensoren: MEMS-basierte Quantensensoren mit Empfindlichkeiten nahe dem theoretischen Limit
Trotz des enormen Potenzials bestehen weiterhin technologische Herausforderungen:
- Zuverlässigkeit: Langzeitstabilität bei extremen Umgebungsbedingungen (Temperaturen von -40 bis +200°C, Vibrationen bis 50g)
- Packaging: Hermeterische Versiegelung mit Leckraten <10⁻⁸ mbar·l/s bei gleichzeitiger Bewegungsfreiheit mechanischer Komponenten
- Skalierbarkeit: Überwindung physikalischer Grenzen bei weiterer Miniaturisierung
- Standardisierung: Vereinheitlichung von Designregeln und Schnittstellen zur Kostensenkung
Mit dem kontinuierlichen technologischen Fortschritt und der Erschließung neuer Anwendungsfelder wird erwartet, dass der globale MEMS-Markt von 14,5 Milliarden USD im Jahr 2022 auf voraussichtlich 34,2 Milliarden USD im Jahr 2028 anwachsen wird, was einer jährlichen Wachstumsrate (CAGR) von 15,3% entspricht.
Fazit
MEMS repräsentieren eine revolutionäre Technologie, die die Grenzen zwischen Elektronik und Mechanik auf mikroskopischer Ebene überwindet. Durch die Kombination von Sensorik, Aktorik und Elektronik auf kleinsten Raum ermöglichen sie neuartige Anwendungen in praktisch allen Industriezweigen. Die kontinuierliche Miniaturisierung, gepaart mit steigender Funktionalität und sinkenden Kosten, bildet die Grundlage für zukünftige Innovationen im Bereich der Mikrosystemtechnik.
Die Integration von MEMS in unser tägliches Leben – von Smartphones über Fahrzeuge bis hin zu medizinischen Implantaten – wird sich in den kommenden Jahren weiter intensivieren. Mit dem Übergang zu noch kleineren Strukturen im Nanometerbereich (NEMS) eröffnen sich zusätzliche Anwendungspotenziale an der Schnittstelle zur Quantenphysik und Molekularbiologie.
Letztes Update des Artikels: 18. März 2025